As is known to all, the bulldozer TRACK ROLLER needs to keep walking slightly under bad working conditions than the excavator TRACK ROLLER, and the operating ratio (the ratio of the running time of the supporting roller and the running time of the main engine) is 10 to 20 times higher than that of the excavator. Therefore, its quality requirements are higher, and the structure is generally different from that of the excavator.
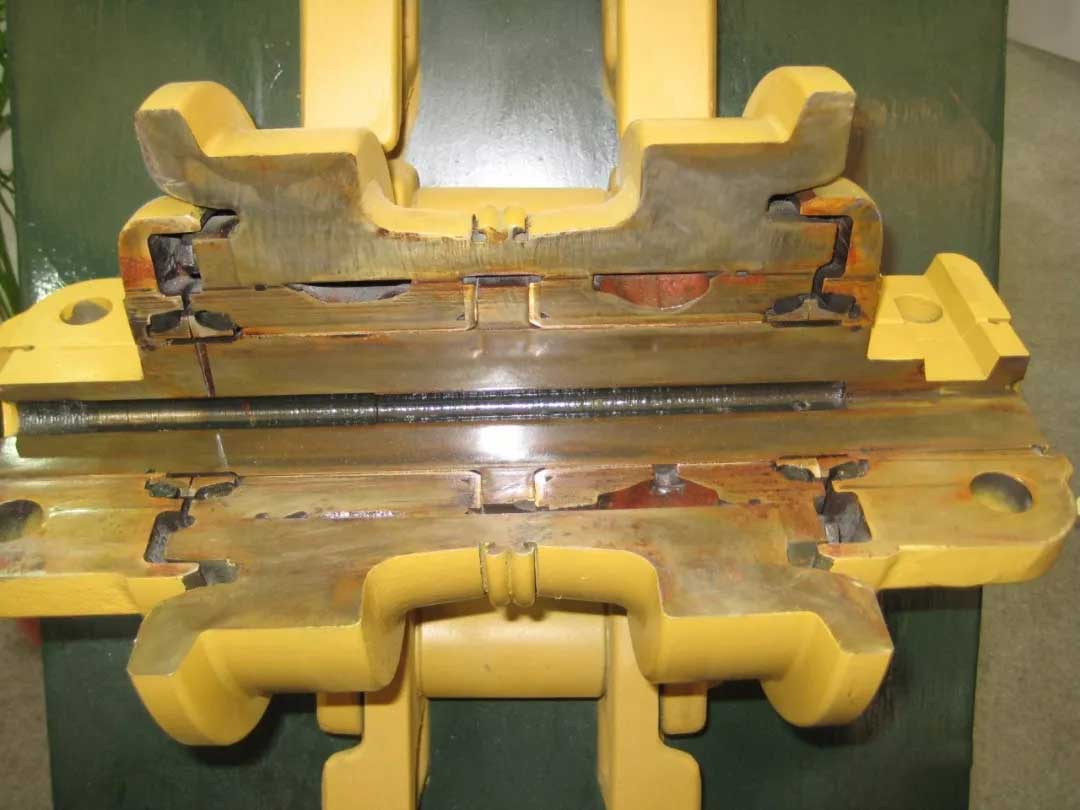
Bulldozer Track Roller Structure
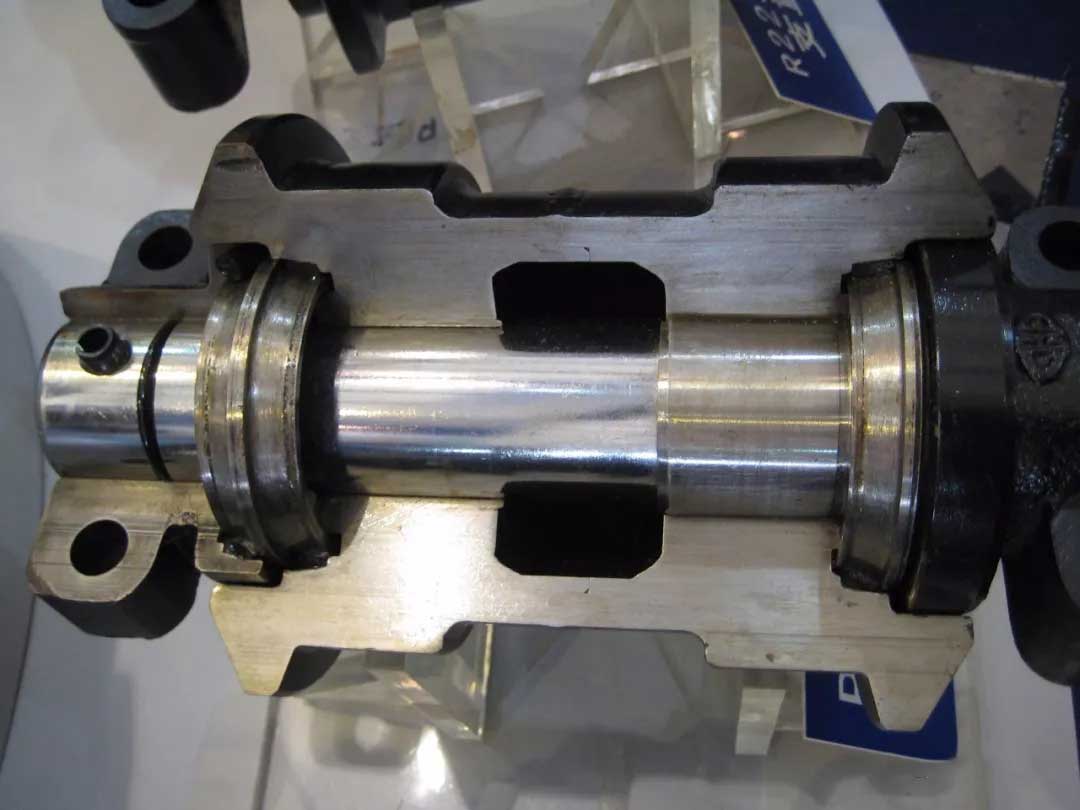
Excavator Support Roller Structure
At present the market bulldozer track roller price difference is very big. Many user also have a difficult choice. We do a simple analysis from the point of view of material technology, mainly a few large pieces, wheel body, cover, ductile iron sleeve, internal bushing, wheel shaft, floating oil seal;
1. Wheel body: the original material is 40Mn2 round steel, and the heat treatment method is overall heating and surface quenching. Many manufacturers use 45 steel or 50Mn billet forging, after intermediate frequency treatment.
2, axle: the original factory for 50Mn quenching and tempering treatment, many cheap products using 45 steel surface medium frequency quenching and tempering treatment.
3, ductile iron sleeve and internal bushing: ductile iron sleeve material for the original factory QT45-10, internal bushing for copper alloy bimetal .In order to reduce the cost, the material is downgraded to HT250 material, and the bushing is made of zinc aluminum alloy.
4. Floating seal assembly: the middle and high-end sealing material is 15Cr3Mo, the service life is the lowest 5000 hours, and the low-end products need seals to reduce the alloy elements, mostly 15Cr1Mo, to reduce the cost.
There are a lot of sellers in the sale of products to the customer weighing to see the weight, do not know the inside of the consumer to see the weight is very heavy that is good product quality but do not know the material replacement of product quality is the biggest harm.
Post time: Apr-12-2021